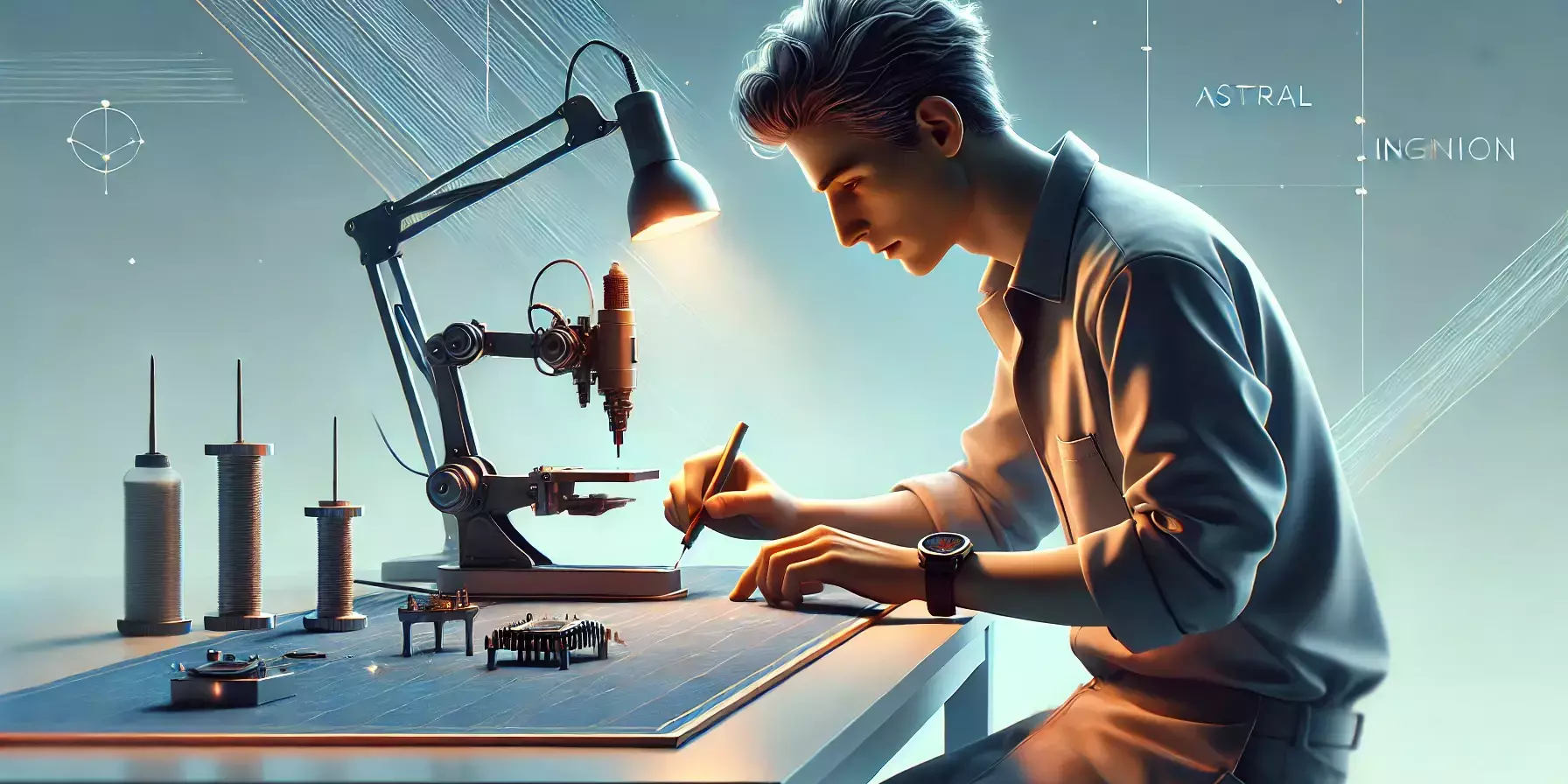
For businesses prioritizing excellence, the quality department is the cornerstone of delivering consistent, defect-free products. As industries become more complex and customer expectations rise, quality managers face mounting pressure to streamline processes, reduce errors, and enhance compliance — all while controlling costs.
Enter artificial intelligence (AI): a transformative tool that’s revolutionizing how quality departments operate. From automating defect detection to classifying data for compliance, AI empowers teams to achieve higher efficiency, accuracy, and consistency.
For early adopters of the AI market, this is an opportunity to lead the way in operational excellence. Let’s explore how AI is reshaping quality management and showcase real-world success stories, including a groundbreaking project that reduced a medical device company’s defect reporting time from weeks to hours.
Why AI Matters in Quality Management
AI enables quality departments to move beyond reactive approaches, empowering them to proactively identify and address potential issues. By leveraging AI, businesses can:
- Automate tedious processes: Freeing up staff for strategic tasks.
- Enhance accuracy: Reducing human error in inspections and reporting.
- Improve compliance: Ensuring data integrity and consistent adherence to regulations.
These benefits are particularly appealing to early adopters looking to modernize their quality management systems and stay ahead of industry demands.
Key Applications of AI in Quality Departments
1. AI-Powered Vision Systems for Quality Inspections
Traditional quality inspections rely on manual checks, which are time-consuming and prone to human error. AI-powered vision systems use machine learning and computer vision to automate defect detection with unparalleled precision.
- How It Works:
- Cameras capture images or video of products during production.
- AI algorithms analyze the visuals to detect defects, anomalies, or deviations from standards.
- The system flags issues in real-time, enabling immediate corrective actions.
- Example Use Case:
- A consumer electronics manufacturer uses AI vision to identify scratches or alignment issues in products, reducing defect rates by 30%.
- Benefits:
- Faster inspections, enabling higher throughput.
- Consistent and unbiased defect identification.
- Reduced waste through early detection of flaws.
2. AI for Data Classification and Compliance
Quality departments handle massive amounts of data, from defect logs to compliance reports. Manually classifying and analyzing this data is labor-intensive and susceptible to errors. AI automates the process, ensuring data is accurately categorized and easily accessible.
- How It Works:
- Machine learning models analyze and classify data based on predefined categories or patterns.
- AI flags anomalies or discrepancies for further review.
- Automated workflows generate compliance-ready reports with minimal manual input.
- Example Use Case:
- A medical device company reduced its annual defect reporting process from 6 – 8 weeks involving multiple staff to just 5 hours, at a cost of less than $500. The solution not only expedited reporting but also ensured higher consistency and accuracy in compliance submissions.
- Benefits:
- Significant time and cost savings.
- Increased accuracy in regulatory submissions.
- Faster access to actionable insights from data.
Real-World Impact of AI in Quality Departments
Case Study: Medical Device Company’s Defect Reporting Overhaul
A medical device company faced a time-intensive defect reporting process that spanned 6 – 8 weeks annually and required input from multiple staff members. By implementing an AI-powered solution, the company achieved:
- Time Savings: Reports generated in just 5 hours, reducing the process by over 90%.
- Cost Efficiency: A one-time investment of less than $500 replaced weeks of manual labor.
- Accuracy Gains: Automated data analysis ensured compliance submissions were error-free and consistent.
This project exemplifies how AI transforms quality management, enabling teams to focus on strategic initiatives while maintaining compliance.
Benefits of AI for Quality Managers
1. Time Efficiency
- Automating inspections and reporting frees up time for quality managers to focus on process improvements and strategy.
2. Cost Reduction
- AI reduces reliance on manual labor and minimizes waste by identifying defects early in the production process.
3. Improved Accuracy
- AI eliminates inconsistencies and human errors, ensuring that quality standards are met without fail.
4. Regulatory Compliance
- Automated data classification and reporting ensure adherence to industry regulations, reducing the risk of non-compliance penalties.
Steps to Implement AI in Quality Departments
1. Identify Pain Points
- Start by identifying the most time-consuming or error-prone processes in your quality workflow.
- Example: Manual defect inspections, compliance reporting, or data classification.
2. Select the Right AI Tools
- Choose AI solutions tailored to your industry and quality management needs.
- Example: Vision systems for defect detection or machine learning models for data classification.
3. Pilot and Evaluate
- Begin with a small-scale pilot project to test feasibility and measure ROI.
- Example: Implement AI for a specific product line before scaling across the organization.
4. Train Your Team
- Provide training to ensure quality managers and staff can effectively use AI tools.
5. Monitor and Optimize
- Continuously evaluate AI performance and refine algorithms to improve accuracy and efficiency over time.
The Future of AI in Quality Management
As AI technology evolves, its applications in quality management will expand further. Emerging trends include:
- Predictive Quality Analytics: Using AI to predict potential defects before they occur, enabling proactive interventions.
- Real-Time Compliance Monitoring: AI systems that automatically ensure adherence to changing regulatory requirements.
- Edge AI for Decentralized Quality Checks: Performing inspections directly on production lines without relying on cloud computing.
For early adopters, staying ahead of these trends ensures sustained competitive advantage and operational excellence.
Conclusion: Embrace the AI Revolution in Quality Management
AI-powered solutions are transforming quality departments, empowering managers to achieve unparalleled efficiency, accuracy, and compliance. By automating inspections, streamlining data classification, and reducing reporting times, businesses can focus on delivering the highest quality products to their customers.
The success of projects like the medical device company’s defect reporting overhaul demonstrates the tangible benefits of AI for quality management. For early adopters ready to lead the way, the time to embrace AI is now.
Step into the future of quality management with AI — where innovation meets excellence.