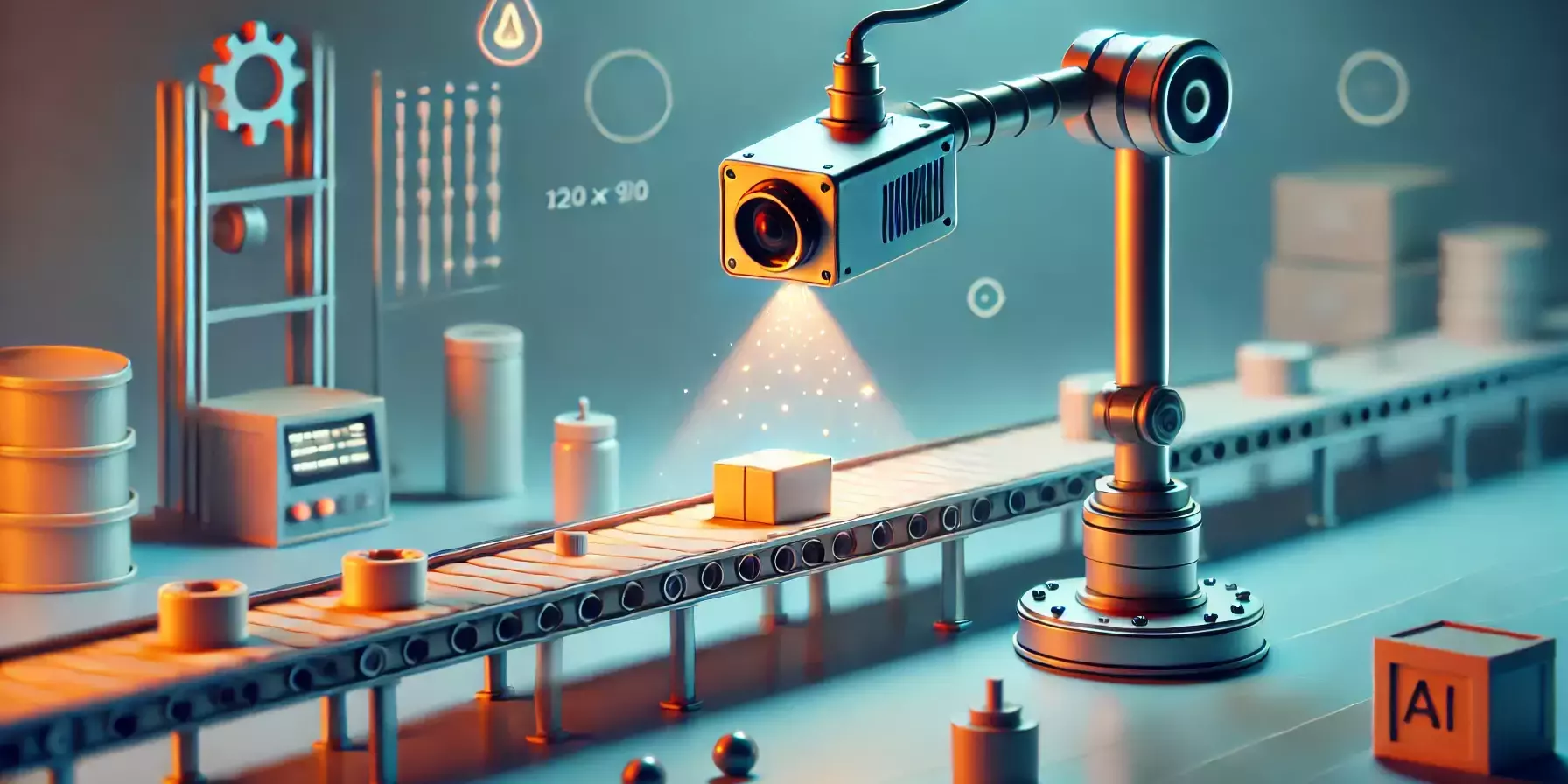
For decades, quality control in manufacturing was a painstaking process. It relied on human inspectors staring at endless conveyor belts, scrutinizing products for defects, and manually sorting out the good from the bad. It worked — sort of. But it was slow, inconsistent, and prone to human error.
Then along came machine vision. With AI-powered cameras and deep learning algorithms, manufacturers could automate defect detection, ensuring faster, more precise, and more reliable quality control than ever before. But is AI truly revolutionizing quality control, or is it another overhyped tech trend? Let’s dig into the reality behind the headlines.
What is AI-Powered Machine Vision, and How Does It Work?
At its core, machine vision is the process of using cameras, sensors, and AI algorithms to analyze images and detect defects or anomalies in manufactured goods. Unlike traditional rule-based vision systems, which required painstaking manual programming, AI-powered systems learn from massive datasets of product images.
Here’s what makes AI-powered vision systems stand out:
- Self-Learning: Instead of relying on predefined defect criteria, machine vision models are trained on thousands (or even millions) of product images, learning to recognize subtle patterns that indicate flaws.
- Speed: While a human inspector might check a few hundred products per hour, AI-powered cameras can analyze thousands per minute, catching microscopic defects invisible to the human eye.
- Consistency: Humans get tired. AI doesn’t. It delivers the same level of scrutiny day in, day out.
Sounds incredible, right? And in many ways, it is. But it’s not without its challenges.
Who’s Using AI for Quality Control? Real-World Examples
Several industries are already deep into AI-powered quality control, with results that range from impressive to downright game-changing.
1. BMW: AI in Automotive Manufacturing
The auto industry has always been obsessed with precision. A single defective component can cause massive recalls, safety hazards, and brand damage. BMW has been at the forefront of AI-powered machine vision, integrating it into assembly lines to spot microscopic defects in car parts.
BMW’s AI-powered system uses high-resolution cameras and deep learning models to inspect weld seams, paint jobs, and part alignments. If a deviation is detected, the system can automatically flag or even remove the faulty part before it progresses further down the line. The result? Fewer recalls, lower waste, and higher customer satisfaction.
2. Coca-Cola: AI for Perfect Packaging
For a company that produces billions of bottles annually, even a 0.01% defect rate can result in millions of wasted products. Coca-Cola leverages AI-powered quality control systems to ensure bottles are properly filled, caps are sealed correctly, and labels are applied with precision.
Coca-Cola’s AI system doesn’t just identify defects — it predicts potential failures. By analyzing production trends, it can detect if a filling machine is starting to show irregularities before it results in a full-scale production error.
3. Foxconn: AI in Electronics Manufacturing
Electronics manufacturing demands extreme precision. A tiny misalignment on a microchip can render an entire device useless. Foxconn, which produces devices for Apple and other tech giants, uses AI-powered machine vision to inspect circuit boards, detect soldering issues, and verify chip placements.
Given the complexity of modern electronics, traditional rule-based vision systems struggled with ever-changing product designs and shrinking component sizes. AI, on the other hand, continuously learns and adapts, improving its detection accuracy over time.
The Challenges of AI in Quality Control
For all its promise, AI-powered machine vision isn’t perfect. It comes with real-world limitations that manufacturers need to navigate.
1. Training Data is Everything
AI is only as good as the data it learns from. If you train a model on perfect, well-lit images of defects, it might fail when confronted with real-world variations — such as poor lighting, dust, or slightly different angles.
Example: A manufacturer using AI to detect cracks in glass found that the system struggled in environments with inconsistent lighting. The model had been trained on clean, high-contrast images, but real-world conditions weren’t so forgiving.
2. High Upfront Costs and Complexity
While AI-powered quality control can save money in the long run, the initial investment is steep. Companies need to:
- Install high-resolution camera systems.
- Train and fine-tune AI models.
- Integrate AI with existing production lines.
For small and mid-sized manufacturers, these barriers can be deal-breakers. AI is great at scale, but for companies producing lower volumes, the return on investment isn’t always immediate.
3. False Positives and False Negatives
- False Positives: AI flags a perfectly good product as defective, leading to unnecessary waste.
- False Negatives: AI fails to detect a real defect, letting a faulty product slip through the cracks.
Fine-tuning AI to balance precision with practicality is a complex challenge. Some manufacturers report high initial error rates, requiring months of retraining before the system performs reliably.
Ethical Concerns: Is AI Replacing Human Jobs?
One of the biggest concerns surrounding AI in manufacturing is job displacement. If AI can inspect products faster and more accurately than humans, does that mean thousands of quality control inspectors will lose their jobs?
The reality is more nuanced. Many manufacturers retrain their workforce to work alongside AI rather than replacing them outright. Instead of inspecting products manually, workers supervise AI systems, handle maintenance, and manage exceptions that AI cannot resolve.
In some cases, AI actually creates new roles—such as AI trainers, maintenance specialists, and system auditors. The challenge for businesses is ensuring that employees are given opportunities to transition into these new roles rather than being left behind.
Is AI in Quality Control Overhyped or Truly Transformative?
So, is AI-powered machine vision the future of quality control, or is it another overhyped tech trend? The truth lies somewhere in the middle.
Where AI is Truly Transformative:
- In industries with high production volumes and tight tolerances, such as automotive, electronics, and pharmaceuticals, AI-powered quality control is already delivering tangible benefits.
- AI is reducing waste, increasing efficiency, and lowering recall rates.
Where AI Still Struggles:
- In environments where defects are highly variable, AI models require constant retraining, leading to high operational costs.
- In small-batch or custom manufacturing, AI may not be cost-effective compared to skilled human inspectors.
For large-scale manufacturers, AI-powered quality control is a no-brainer. But for smaller operations, the decision isn’t so clear-cut. The key is to evaluate whether AI truly aligns with the company’s production model and long-term goals.
Final Thoughts: AI as a Tool, Not a Silver Bullet
AI-powered machine vision is reshaping quality control in manufacturing, but it’s not a magic solution. It excels in high-volume, repetitive environments, but it still requires human oversight, data refinement, and continuous improvement.
Manufacturers should view AI as a tool, not a replacement for human expertise. The best outcomes will come from AI-human collaboration, where machines handle the repetitive tasks and humans focus on higher-level problem-solving.
For companies that invest wisely, AI in quality control isn’t just the future — it’s already here. The question isn’t whether it works, but how well companies can adapt and integrate it effectively.